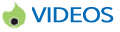
Langage AD - Drying reject from AD plant - Runi SK370
At Langage Farm AD they bring in food waste for their biodigester to produce biogas. The biogas is used to generate electricity for their production of dairy products, whereas the digestate is used as fertilizer on their fields to create a closed loop. See how the RUNI SK370 dries the wet, rejected packaging that comes with the food waste in their AD plant, achieving a 50-60% reduction in the overall weight of the liquids. This leads to significant cost savings for Langage AD.
An interview with Andreas Krieg on the advantages of fermenting sugar beet waste (sugar beet pulp) year-round in biogas plants as a solution for energy generation and CO2 compensation for the sugar industry.
The depackaging machine DRM separates and processes organics waste loke food waste. It separates the organic and inorganic substances right at the beginning of the material processing in almost one process step. With Tietjen's depackaging equipment DRM, the organic waste is separated and the foreign and impurities are removed at the same time. This means that less effort is required for depackaging and waste separation.
Never recalibrate, worry about drifting, deal with constant maintenance or have to second guess your sensor's accuracy with MoistTech's NIR equipment.
All our sensors are instant with hundreds of points of data measurement per second providing you with real time accurate measurements. MoistTech is a one-time calibration with a no drift optical design to ensure the accuracy and repeatability needed. MoistTech Corp has the expertise to assist you in your moisture measurement and control needs, increasing productivity and reducing waste. Customers have reported 400% or more increases in production efficiency & we provide 30-day service guarantees! info@moisttech.com
Biogas plants need a reliable feed for high-performance operation. At the same time, biogas plants are getting bigger and bigger. This is where the new biomass shredder BMS from Tietjen comes in. The vertical biomass shredder BMS 1500 handles more than 15 t biomass per hour and is thus one of the bio grinders with the highest throughput on the market.
Every manufacturer knows that if you want to make a #profit, it is imperative that you keep your costs down. Wasted raw materials are an issue for most companies but with MoistTech's IR 3000 #MoistureSensor, you can reduce waste and increase your company's profits.
info@moisttech.com / 941-727-1800 / +44 1138680413
No matter what industry you're in, moisture measuring sensors can help improve your products. MoistTech Corp looks to make your job easier by providing moisture sensing technology for all types of industries and production facilities.
Krieg & Fischer operate independently of subcontractors and can develop and implement the best technical and economical solution for your particular application. We place emphasis on the fact that there is no specific K&F procedure. Here we primarily focus on the input material and the conditions on site. This is the only way to develop an optimized system for your biogas plant.
The Paddle Depacker is able to depack a wide variety of food waste products and produce a very clean organic output (official lab results above 99,5% clean organic soups).
The Separation Mill DRM depacks food waste. It separates the organic and inorganic substances right at the beginning of the material processing in almost one process step. With the Separation Mill DRM, the organic waste is separated and the foreign and impurities are removed at the same time. This means that less effort is required for depackaging and waste separation. Process steps such as manual sorting, re-shredding and various other screening techniques are no longer necessary.
The energy-saving UNTHA Eco Power Drive with water-cooled synchronous motor saves up to 75 % energy costs with increased efficiency in comparison to conventional diesel-hydraulic drive variants. The shredders for waste wood processing offer a throughput of up to 40 t/h smaller 100 mm. UNTHA's specially designed waste wood package consists of indexable inserts that may be reversed up to 4 times and perforated screens with chip breakers, ensuring a long service life and a particularly homogeneous final product without excess lengths. In addition, the quick-change screen system makes it easy to swap the perforated screen when a new input material is introduced. Test the XR directly at your location: https://www.untha.com/p/trial
Construction work at a Norfolk (UK) -based anaerobic digestion (AD) plant will provide households in the south-east town of Attleborough with 10MW of biomethane per hour - enough to supply 4,000 homes, and guarantee green gas for most of the year.
A plant in Le Puisot, France has installed a membrane upgrading system for the production of biomethane using biogas produced with the waste from nearby farms (such as manure) and agro-industrial waste. The biomethane produces (300 m3/hour) which is fed into the GRDF national gas network.
The first bio-LNG plant in the Netherlands will produce an estimated 3.4 kilotons of bio-LNG per year. This amount of bio-LNG is sufficient for 13 million on-road kilometers, and prevents the emission of more than 14.3 kilotons of fossil CO2.
BrewDog, one of the largest Scottish craft breweries, is officially the first carbon negative beer brewery in the world. This, thanks to an investment plan including the start-up of a biogas plant at the brewery's Ellon plant, fuelled with waste from beer processing, which will not only convert production wastewater into clean water, but will also produce biomethane, organic fertilizer and CO2 for food use.
Pomace is a by-product that can be used for the production of biogas, particularly in countries like Italy.
There are several stages between the production of biogas in an anaerobic digester and the injection of biomethane into the national gas grid. Learn more about this process by watching this video from our friends at Biogas Channel who visited a membrane upgrading plant in Northern Italy, which processes 1200 Nm3/h of agricultural biogas!
Shell New Energy is the Shell brand providing innovative and clean energy solutions. Shell New Energy invests two billion dollars annually to support the dissemination of alternative fuels, including LNG and Bio-LNG. To this end, the company is working on several biomethane projects, including three prominent initiatives in Brazil, India and the Netherlands, as explained by Christian Cuenot, Business Developer and Manager at Shell New Energies.
Installed in 2007, the plant was the first in the area to produce biomethane and inject it into the existing natural gas network. Every year, approximately 46,000,000 kWh of biomethane produced covers one third of the area's heating needs, equal to the consumption of about 2,200 families! Here's a closer look at the plant.
Under the Greek sun, in the heart of Macedonia, stands a 1MW biogas plant, generating 8,500 MWh of electricity and 6,500 MWh of thermal energy. The plant, which has been operating since 2016 and is owned by LAGADA S.A., is powered 70% by animal waste, 1.5% by energy crops and the rest by waste from the agricultural food industry. The plant offers numerous benefits, including a reduction in CO2 emissions of around 600 tons a year.
IVECO has been investing in the biomethane sector for many years and is well-aware of the benefits that the fuel can offer. Although many large companies like Ikea, Carrefour, Coca Cola and Nestlé have set an example by using biomethane-powered goods vehicles, there are still many barriers to be overcome in this sector including the availability of suitable filling stations. You can find more details in this interview given by IVECO at this year’s EBA Conference from the Biogas Channel.
The French VOL-V Group recently unveiled a biogas plant in the Montauban-de-Bretagne area, département of Ille-et-Vilaine. The plant has the capacity to reclaim 36,000 tonnes of organic by-products per year.
Producing biomethane can be a challenging process. Here's an interesting video explaining what it's all about.