Fre-Energy continues journey as “biogas innovators”
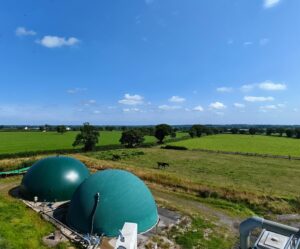
In that time, its co-founder, Chris Morris, has seen the good, the bad, and the ugly in terms of running plants, and has developed a sixth sense of what will and will not work. The company’s own AD plant is Lodge Farm in Holt, which is used as a research and development site.
Its feedstock of food waste comes from local restaurants and primary food manufacturers (sausage makers, creameries, bakeries), with the occasional tanker of slurry to ‘keep the bugs topped up.’
Fre-Energy began life in 2009, but its founders' experience with biogas began much earlier. In 1998. Chris worked on an AD plant in Avonmouth, and was impressed with how clever it was in dealing with waste. A while later when nearby farming friends, the Tomlinson family, were looking at slurry solutions, together they explored biogas as a viable option.
Their research concluded that, whilst they liked what AD did, a lot of the plants weren’t fully engineered or even maintained. Some had been running for 30 years with few improvements, and many had problems with grit and stones, particularly when cattle had been bedded on sand.
“What we saw was very hobbyist,” says Chris. “With the greatest intentions farmers had built plants to manage slurry and generate power to their farms, but they weren’t specialists. And why would they be? Their job is to produce food, not energy.
“We saw a real gap in the market for biogas to be done well using waste as a feedstock. Our vision as a plant builder was to do as much or as little as people wanted. But we wanted to prove ourselves with our own AD plant first. This was the start of our journey as biogas innovators; we built a prototype de-gritting system initially, then moved on to building a generator that could cope. Thankfully technology has moved on and there are generators available now, but in the early days, we had to rely on our own creations.
“However, right from the beginning we used Vogelsang equipment; their rotary lobe pumps and solid matter feeder systems were and still are the best machines for the job. But what sets them apart for us is the service they give. If we have an issue or need replacement parts, they’re able to help us straight away, which has been immensely valuable over the years.”
Having worked with dozens of biogas sites, Chris believes there is a formula to make a site flourish and it comes down to its principal use. Fre-Energy’s most successful sites have been built to complement the farm, not built to give to the grid.
If built the other way around - to meet a certain power target - often farmers or plant operators are left struggling to source feedstock for their digesters and the plant performance fails. Either because there isn’t enough to feed the digesters, or the bacteria-balance is harmed from using stock that the plant wasn’t specified for. Fre-Energy has navigated this by designing plants that can accommodate ‘opportunist’ waste, allowing for more flexibility of the feedstock.
“We see a lot of AD plants on farms that are too big for their needs. They’re often sized to hit the maximum tariff regardless of the feedstock available. “The exception is gas-to-grid specific sites, where the capital and operating costs of the equipment dictates large plants, typically 2MW and greater,” explains Chris. “But farmers are often advised that this is best and are at the mercy of those who are advising them or providing funding.”
An example of a plant designed to ‘fit the farm’ is Ystym Colwyn Farm, Powys. Built in 2019 by Fre-Energy to provide heating for 325,000 broiler chickens and power the farm buildings using only farm waste (16,000 tonnes of slurry, 5,000 tonnes of chicken litter, 1,500 tonnes of silage and 1,000 tonnes of farmyard muck). The AD plant generates 4,262 Mwh of which just 23 per cent is used to power the farm. The rest goes to the grid.
“Exploring methods of low carbon farming is an important part of farming’s future,” says Ed Gittins, farm owner. “Going forward, we’re aiming to use an anaerobic digester to produce biogas to power our tractors and other farm machinery too.
“When Fre-Energy designed our plant, they specified Vogelsang’s PreMix solid matter feed system. It’s been an excellent system for us. The equipment is strong and works hard, particularly as we have a varied feedstock and can’t guarantee it is free from stones and other foreign matter. When this happens, the debris removal system separates these so they don’t make their way into the pumps and damage them.”
According to Fre-Energy, a strong indicator of how well a biogas plant will perform long-term is down to how the farmers themselves run the AD plant as a whole, and treat each component of the machinery.
“Preventative maintenance is key,” says Rob Morris, system-designer at Fre-Energy. “It’s a bit like servicing a car will keep it running smoothly and save money in the long-run. Unintended down time is another big cost that’s usually due to contaminated feedstock. Gate hangers, barbed wire and bailer twine are a nightmare to unwrap from the interior of a pump.”
Sizing the equipment during the design-stage is also important to get right. To save on start-up costs, some sites have under-sized equipment, only to find that the machines have to work harder to macerate, pump and heat feedstock. These undersized components subsequently wear out quickly or need a higher turnover of replacement parts than budgeted for. “Don’t cheap out,” is the message from Rob.
So, what is in the future of the UK biogas market? Waste, according to Chris.
“There isn’t a huge amount of innovation in crop feed, but there is in waste. We’ve also seen a pushback in the use of crops as an AD energy source, and there can be some distortions of ‘green economics’ where people haven’t considered the cost to grow the crops in the first place. They might mean well, but growing crops as an energy source can have an impact on food prices. I think there’s a balance to be had.
“I think the future of AD, currently splits two ways: very large plants chasing the tariff for RTF (Road Fuel Tariff), gas to grid and valorising the carbon dioxide from the biogas. And small farm-based plants looking to utilise the on-farm and local inputs to reduce CO2 emissions, provide valuable fertiliser and some ‘green energy’. The challenge is to provide robust reliable technology at the small scale.”
Chris adds: “We always set out to be a food waste site here at Lodge Farm, and it’s been a success from day one. But food waste does come with increased operating, legislative and regulatory costs, so we need to charge a gate fee to make that cost back. A farm-based AD plant operating using farm-based inputs typically requires one person for 25% of a day to operate. Our food waste plant uses typically 1.5 people to operate.”
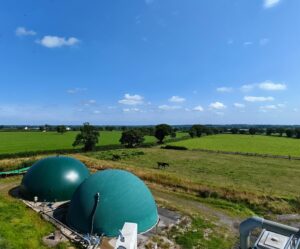